Lithium recovery and reuse from batteries (*WNWNW #2)
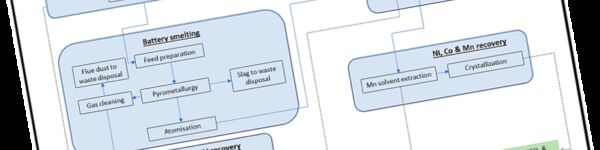
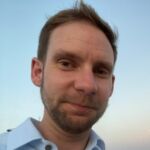
Bart Verrecht, Senior Program Manager Battery Recycling at Umicore, considers the current technologies for recycling lithium batteries.
Prior to his current role, Dr Bart Verrecht spent over four years in membrane research, industrial wastewater treatment process design/optimisation, and business development. For the past five years, he has worked for the circular materials company Umicore. He has recently co-authored a paper in this field.
Waste Not Want Not Wednesdays #2: the two options for recycling of Li ion batteries, and the true environmental benefit*
1. Sustainable battery recycling?
Battery recycling has been all over the news in the past few years, with grand ambitions and major investments announced by startups and incumbent companies alike. Lately however, the market has cooled down, as short- and medium-term growth projections for the European electric vehicle (EV) market have been scaled back substantially. As a consequence, some companies – including BASF, Umicore and Eramet – have delayed or even shelved their investment plans in battery recycling.
2. Long-term demand for critical raw materials
Despite this slowdown, the long-term expected growth in electric mobility will still require vast amounts of critical raw materials such as nickel, cobalt and lithium. During battery production, large amounts of production scraps are generated, especially when new cell makers ramp up their production. Furthermore, increasing numbers of EV batteries will reach their end-of-life in the coming decades. To keep these critical raw materials in circulation, we need to develop and industrialize sustainable battery recycling solutions that recover and transform them back into ‘battery grade’ building blocks for new cathode materials.
3. Battery recycling approaches
Battery recycling typically falls into two main categories.
The first is often referred to as ‘Pyro’ but, in reality, it is a combination of pyro- and hydrometallurgy. In the first step, batteries are smelted at high temperatures in a pyrometallurgical process to concentrate the valuable metals such as Ni, Co and Cu in a pure alloy and Li in the flue dust. In a second step, the alloy and Li flue dust are further refined in a hydrometallurgical process.
The second approach is often called ‘Hydro’. In this case, it is a combination of a (thermo-)mechanical pretreatment step and a hydrometallurgical refining process. The (thermo-)mechanical step includes an optional heat treatment, shredding and separation to create what is known as 'black mass' that contains most of the valuable elements (Ni, Co, Cu, Li) but that also still includes impurities (carbon from the graphite and electrolyte, fluorine compounds, Cu/Al foil fractions, etc.). Further hydrometallurgical refining is needed to extract the valuable metals from this complex mixture.
4. A nuanced reality
So in practice, battery recycling is not simply a choice between ‘Pyro’ or ‘Hydro’. Both methods involve multiple steps: a certain type of pretreatment (pyrometallurgy vs (thermo-)mechanical pretreatment), followed by a hydrometallurgical process. The key distinction between the two methods is that the pretreatment step is much more effective in one of the processes compared to the other.
Pyrometallurgical pretreatment is the most complex but also the most effective method. It leads to a high quality and purity of the intermediates, thereby reducing the cost and complexity of the hydrometallurgical process. In other words, the pure alloy and Li flue dust only need simple hydrometallurgical processes to transform them to battery grade end products and allow for high recovery yields of the valuable metals (these being Li, Ni, Co and Cu).
(Thermo-)mechanical pretreatment (used in the 'Hydro' approach) is easier and requires less investment. However, the quality, composition and metal recovery yield of the black mass depend very much on the material entering the shredding facility. The hydrometallurgical refining of this black mass is more complex and expensive due to the remaining impurities it still contains.
5. Sustainability and carbon footprint
This brings us seamlessly to sustainability and carbon footprint. Here it’s also a nuanced story: recent analysis (Van Hoof et al., 2023; Figure 1) showed that ‘Pyro’ battery recycling results in a lower overall carbon footprint than ‘Hydro’. However, the two approaches have very different carbon emission profiles:
- ‘Pyro’ results in higher direct (‘scope 1’) emissions due to the use of graphite as a reducing agent, while also delivering energy to the process. However, this is compensated by lower indirect (‘scope 3’) emissions, because the pyro step enables the simpler hydrometallurgical step that follows, requiring less chemical reagent.
- ‘Hydro’ has lower direct emissions, but has higher indirect emissions. This is because of the more complex hydro flowsheet that uses more chemical reagent. Additionally, the graphite ends up in the leaching residues and is typically incinerated in a waste incinerator or used as a reducing agent in the steel industry – ultimately ending up as CO2 as well.
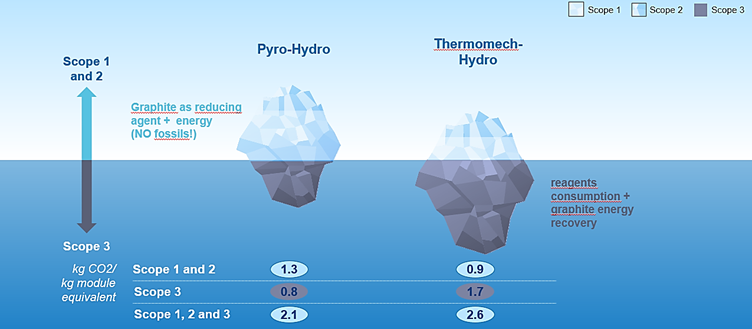
So this begs the logical question: if the fate of graphite drives so much of the indirect CO2 emissions, why not just recycle it as well and avoid these emissions?
Graphite recycling is indeed a potential avenue to improve further the sustainability of battery recycling, and this has been a focus of significant research efforts recently by both academia and startups. However, graphite recycling is still at a relatively low Technology Readiness Level (TRL). More importantly, we must consider whether it actually makes sense economically and environmentally to recycle it back to battery grade graphite. Indeed, it is not because it is technically possible that it also represents a sustainable reality.
6. The bigger picture: recycled versus mined metals
Beyond comparing CO2 emissions of different recycling approaches, the bigger question is: How does the carbon footprint of recycled metals compare to the carbon footprint of mined (primary) metals? To answer this, it is important to look not only at the CO2 burden of the recycling process, but also to the credits gained by recovering Ni, Co, Li and also Al and Cu from the batteries (e.g. from battery casings and wiring).
An analysis by Van Hoof et al. (2023, see Figure 2) shows that when taking these credits into account, battery recycling achieves a net negative carbon footprint. This means that the environmental benefits of recycling metals outweigh the emissions associated with the recycling process – making battery recycling clearly advantageous over mining of primary materials.
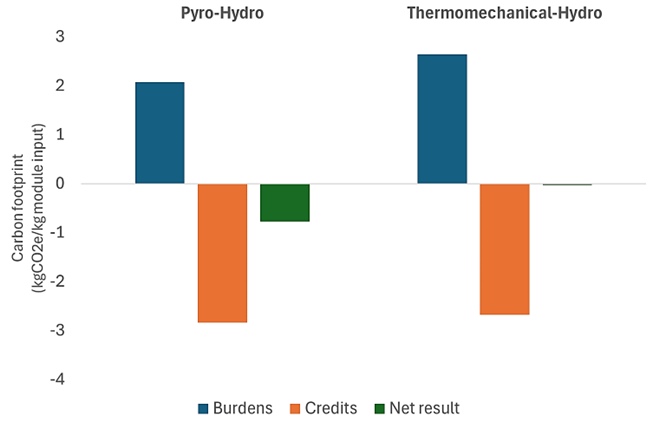
7. Sustainability beyond carbon footprint
Of course, sustainability is not just about carbon footprint. Other aspects, e.g. resource depletion, land usage, etc. must also be taken into account, but that is a much bigger discussion. There are additionally technical limitations on harvesting natural resources – with lithium being a key example. Natural sources of lithium are plentiful: the total amount of lithium in seawater – around 230 billion tonnes – is almost inexhaustible. However, the high salinity and extremely low concentrations of lithium (<0.2 mg/L) make this source practically unviable, based on the current technologies used to recover lithium from spent battery processing leachate.
8. Conclusion
Battery recycling delivers recycled metals with a net negative carbon footprint, making battery recycling more sustainable than mining. Also, and perhaps more importantly, maximizing local battery recycling will reduce reliance on mining of additional critical raw materials over time, making Europe less resource-dependent on other parts of the world. However, to fully realize this potential, we need a level playing field, facilitated by a strong and enforceable EU Battery regulation. And that is yet another discussion …