Membrane recycling (*WNWNW #4)
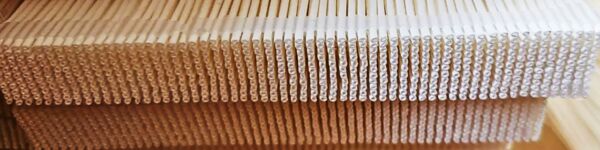
Simon Judd has over 35 years’ post-doctorate experience in all aspects of water and wastewater treatment technology, both in academic and industrial R&D. He has (co-)authored six book titles and over 200 peer-reviewed publications in water and wastewater treatment.
Waste Not Want Not Wednesdays #4: the viability of recycling membranes*
1. Membrane life
A subject that has started to receive more attention as a result of recent moves by EU legislators to ban PFAS products is that of recycling membranes at the end of their life. Recycling goes some way towards reducing the amount of polymer that needs to be manufactured − the polymer being the most significant potential source of PFAS omissions in the life cycle of a PVDF membrane − as well as reducing the amount of PFAS material for disposal. So, how viable is reusing membranes which have been irreversibly fouled, clogged and damaged by years of exposure to cleaning reagents like chlorine?
Well, first of all, some membrane materials − notably ceramics − are not significantly degraded by chemical cleaning. This being the case, it may not be necessary to recycle ceramic membranes, provided their life can be extended through appropriately aggressive physical and chemical cleaning. Such cleaning would be expected to limit the accumulation of the more tenacious of the membrane surface fouling and channel clogging materials.
The real target of recycling is likely to be the PVDF membranes. So, how can this be done and, crucially, is it worth the effort?
First, let's examine what constitutes the end of the useful life of a membrane. The factors determining this can be categorised as:
- physicochemical damage to the membrane − such as fibre breakage, pore collapse/shrinkage or loss of hydrophilicity
- physical damage to the membrane module components − such as the seals, connectors, intra-module aerators (if fitted) or linings, and
- irrecoverable fouling from the accumulation of foulant materials (colloidal organic matter, metal oxides, etc) within the membrane pores.
The last of these is perhaps the most difficult to assess. The idea of chemical cleaning is that it recovers the so-called 'irreversible' fouling. However, it is generally recognised that the chemical cleaning itself contributes to the physical deterioration of the membrane. This occurs both through the slow leaching of the hydrophilising agent (Robinson and Bérubé, 2020; Zheng et al, 2023) and the chemical attack of the base membrane material. Chemical attack can take the form of, for example, alkaline hydrolysis (Chheang et al, 2022) and oxidation (Lye et al, 2021) - though the latter appears to apply only to the hydrophilising agent (Oliveira Filho et al, 2021; Li et al, 2022). At some point, therefore, the membrane becomes unusable due to physical damage and chemical denaturisation of the base material, where denaturisation produces hydrophobicity. At this stage, there would seem to be no option but to either replace or, possibly, reprocess the polymeric material.
2. Recycling
As far as actually recovering and reusing the damaged membranes is concerned, most of the focus so far appears to have been on the reuse of reverse osmosis (RO) membranes for nanofiltration (NF) or ultrafiltration (UF) (Veza & Rodriguez-Gonzalez, 2003; Lawler et al, 2013; Garcia-Pacheco et al, 2018). This is compelled by the eye-watering ~2m RO elements that reach their end of life (EoL) every year, and which are currently largely landfilled.
The principle of the recycling−repurposing process is that the ultra-thin polyaromatic amide layer providing the salt rejection on the RO membrane is largely denaturised or removed by oxidation with chlorine to expose the presumably intact supporting UF layer beneath it. This is all very commendable, but RO membrane elements are almost exclusively spiral wound in configuration whereas MF/UF membranes used in potable water and wastewater filtration are predominantly hollow fibre − through many MBR membranes are flat sheet.
In the case of recycling UF/MF membranes that have reached their EoL, a few studies have demonstrated the regeneration of EoL PVDF membranes using selected organic solvents, including so-called 'green' solvents with a reduced environmental impact (Tian et al, 2023). However, the use of these green solvents, and specifically PolarClean®, appears to provide only removal of irreversible fouling. This does not appear to address the loss of the hydrophilising agent and will certainly not repair physically damaged membranes. In such instances, only dissolution of the spent PVDF polymer in an appropriate solvent followed by recasting of the hollow fibre or flat plate membrane can provide a usable product.
This then begs the question: 'How much more environmentally friendly is a polymeric membrane fabricated from recycled rather than virgin material?' The recycled membrane does not deplete existing sources of vinylidene fluoride (VDF), and also avoids the VDF polymerisation step where the risk of PFAS release is at its highest. However, non-green solvents are then needed in the fabrication of both the recycled and virgin membrane.
There is additionally the issue of risk to consider. For the recycled membrane to be acceptable it would have to demonstrate the same level of reliability and robustness in its performance as the virgin material. It is highly unlikely that a recycled membrane, produced by reprocessing a used polymer material, could ever be acceptable for use in potable or water reuse applications. So, there’s a pretty significant marketability issue.
3. Extending membrane life
All of which suggests that the most viable means of reducing the environmental impact of a PFAS-containing membrane is to … make it last longer. This might seem a little flippant, but the humdrum reality is that, whereas there is a plethora of academic research into resilient, fouling-resistant, and generally uber-tough membrane materials, there is very little on effective pretreatment. And yet most site operators will attest that the most serious damage to the membrane and module – including irreversible fouling and clogging – is from hydraulic shocks and/or ingress of extraneous materials which have no business entering the process in the first place.
So, rather than trying to find ways of recycling them, or developing membranes that withstand anything you throw at them, why not just avoid throwing those things at the membrane in the first place? Shock loads can be mitigated by investing in equalisation. Problematic solids can potentially be removed by enhanced screening and degritting, or possibly high-rate (ballasted) sedimentation. Fouling can be reduced by operating at lower flux – which would mean investing in more membranes – but if they required less aggressive cleaning and lasted longer as a result, there may even be an overall cost benefit as well as a reduced environmental impact.
This may all be over-simplistic. The design fluxes and pre-treatment specifications of membrane technologies in water and wastewater treatment have been established as a result of decades of practical experience. But the ground is shifting. Legislation changes, influent loads increase, and gate fees for landfill disposal continue to rise – in some areas, astronomically. It’s often assumed – certainly by much of the academic community – that the membrane represents the pinch point of the process. Perhaps it’s time to assume differently.